
PK: Czy teraz wciąż zdarza się Pani wykonywać takie zlecenia?
Teraz nie podjęłabym się już takich projektów. Dobrze się zastanawiam, zanim zdecyduję się zrealizować jakieś zlecenie indywidualne.
Robiłam na przykład szopkę – dosłownie szopkę [śmiech]. Był Józef, Maryjka, Jezus i zwierzątka w szopce. Zamówił ją taki starszy Pan, który miał może 70 lat. Na początku sądziłam, że uda mi to zrobić w taki bardzo minimalistyczny sposób. Niestety okazało się, że Pan chce, żeby wszystko było bardzo realistyczne.
Bardzo źle wspominam ten projekt. Byłam tak niezadowolona, że wykasowałam wszystkie jego zdjęcia – nie ma po nim śladu [śmiech]. To był chyba taki najbardziej groteskowy projekt i chyba też najbardziej nudny.
PK: Czyli w tej chwili nie realizuje Pani projektów indywidualnych?
W tej chwili raczej nie zdarza mi się to często. To jest bardzo wymagające, dlatego podejmuję się takich zleceń jedynie jeśli to jest klient bardzo konkretny. Trzeba zdawać sobie sprawę, że przy produktach z porcelany efekt finalny jest mocno uzależniony od techniki – nie da się zrobić wszystkiego.
PK: Czy może nam Pani opowiedzieć nieco więcej o procesie powstawania porcelanowych przedmiotów? Jak to wygląda krok po kroku?
Pierwszym krokiem jest to że tę porcelanę należy najpierw przygotować.
PK: A czym tak właściwie jest porcelana?
Porcelana jest rodzajem ceramiki. Ceramika jest takim pojęciem ogólnym, które określa całą dziedzinę. Porcelana jest natomiast materiałem, który się w tej dziedzinie mieści. Jest to materiał bardziej szlachetny niż glina. Jest on połączeniem glinki kaolinowej, skalenia i kwarcu.
Porcelana ma kolor biały, mogą to być różne odcienie bieli, nigdy nie są to kolory takie jak brązy i szarości, które kojarzymy z gliną. Plusem tego materiału jest to, że przed jego wypaleniem widzimy już jego finalny kolor. Masa porcelanowa jest barwiona przed wypaleniem i jest bardzo małe prawdopodobieństwo, że podczas wypału te kolory ulegną zmianie. To jest coś, co zdecydowanie ułatwia mi pracę bo wiem, czego się spodziewać kiedy otwieram piec. W przeciwieństwie do kolorowych szkliw, które nie tylko zmieniają swój kolor podczas wypału, ale też lubią płatać figle.

PK: Na czym w takim razie polega przygotowanie porcelany?
Pracuję z porcelaną, która ma formę płynną. Taka porcelana ma najpierw formę proszku, dlatego też należy ją przygotować. Żeby to zrobić zalewam tę masę wodą i odstawiam do specjalnych beczek. Później przez około miesiąc taka porcelana stoi sobie w beczkach a ja od czasu do czasu ją mieszam, żeby pozbyć się pęcherzyków powietrza. No i w momencie kiedy masa już jest gotowa to mogę zaczynać produkcję.
Ze względu na to, że proces przygotowania materiału jest długi, zazwyczaj planuję to w taki sposób, żeby zawsze mieć kilka takich beczek przygotowanych do produkcji. To dlatego, że tak naprawdę nigdy nie wiadomo jakie projekty się pojawią, jakie będą zamówienia i jaka dokładnie ilość masy będzie potrzebna.
Kiedy zbliża się termin produkcji lub wysyłki wyciągam ją z beczek i zabieram się do pracy. Wtedy ta masa musi być już dobrze odpowietrzona, tak żebym była pewna, że można z niej korzystać.
PK: I co dzieje się potem?
W tym momencie możemy tak naprawdę wlewać porcelanę do wcześniej stworzonej formy. Taka forma musi być przygotowana wcześniej, ponieważ jeśli nie jest zupełnie sucha, nie możemy wlać do niej porcelany. Ciekawe jest też to, że ta forma nie może być zupełnie nowa – kiedy korzystamy z nowo powstałej formy to zazwyczaj pierwsze kilka sztuk produktu nie wychodzi.
PK: Dlaczego się tak dzieje?
Powodem jest to, że na powierzchni formy wciąż znajdują się jeszcze resztki mydła, którego używamy do zabezpieczenia modelu z którego taką formę ściągamy. Mydło sprawia, że elementy się do siebie nie przyklejają, ale niestety nie jest się go potem łatwo pozbyć, stąd taki skutek.
Jeśli korzystamy ze starszej formy, którą już wykorzystywaliśmy do produkcji to taki problem nie występuje. Natomiast forma nie może być też zbyt stara, ponieważ z czasem staje się ona mniej dokładna. To nie oznacza, że przy pomocy takiej formy nic nie da się już zrobić, natomiast produkty powstałe w zużytej formie wymagają wprowadzania większych i bardziej czasochłonnych poprawek.
PK: Mamy więc gotową masę i gotową suchą formę, która załóżmy była wcześniej używana, co dzieje się dalej?
Następnie taka masa musi być przelana przez sitko, żeby nie było tam żadnych grudek. Wlewamy naszą masę do formy gipsowej a następnie czekamy aż osadzi się na ściance gipsu.

PK: W jaki sposób ta porcelanowa masa osadza się na ściankach formy?
Gips jest materiałem o właściwościach higroskopijnych, to znaczy, że wchłania on wodę. Dzięki tej właściwości, tak zwana “część właściwa” wlanej do formy masy osadza się na jego ściankach. Natomiast ta część masy, która się nie osadza zostaje na dnie i jest następnie wylewana.
PK: Jak długo trwa taki proces osadzania się masy?
To zależy od wielu czynników. Choćby od tego w jakim stanie jest forma, czy jest mokra czy sucha itd. Musimy poczekać aż zobaczymy, że grubość osadzonej masy jest odpowiednia. Moje produkty mają zazwyczaj stosunkowo grube ścianki, więc ten czas oczekiwania jest odpowiednio dłuższy.
PK: Czyli w tym momencie czekamy aż masa osadzi się na ściankach tworząc porcelanową powłokę o odpowiedniej grubości i następnie wylewamy pozostałą jej część.
Tak wylewamy nadmiar masy a następnie odwracamy formę do góry dnem i czekamy aż masa wyschnie w środku. Kiedy widzimy, że porcelana osadzona na ściankach formy robi się matowa wyciągamy produkt.
PK: W jaki sposób wyciągamy produkt z formy?
Po prostu – możemy go wyciągnąć bez problemu, ponieważ w miarę upływu czasu masa porcelanowa kurczy się. Po wyciągnięciu z formy musimy poczekać aż produkt zdębieje.
PK: Co to znaczy?
Produkt zdębiały to taki jest troszeczkę wysuszony inie zmienia kształtu w momencie, kiedy my go chwycimy. W takie dni kiedy jest bardzo ciepło, zazwyczaj trwa to około godziny.
PK: Mamy więc już coś co przypomina w jakimś stopniu finalny produkt. Co dzieje się później – czy to jest etap kiedy wkładamy taki produkt do pieca?
Jeszcze nie. W momencie wyciągnięcia porcelany z formy, kilka kroków wciąż dzieli nas od włożenia wypalania w piecu. W tym momencie łączymy elementy. Jeśli nasz produkt to na przykład kubek z uszkiem, to mając kubek musimy teraz odlać również uszko a następnie połączyć te dwa elementy

PK: Czy to jest praca z kilkoma takimi produktami symultanicznie czy raczej wykonuje pani jeden egzemplarz od początku do końca i dopiero następnie przechodzi do kolejnego?
Pracuję symultanicznie nad kilkoma egzemplarzami – Zazwyczaj planuję to w taki sposób aby mieć na przykład jeden dzień, który poświęcam wyłącznie na odlewanie elementów itd.
PK: Czyli po wyciągnięciu produktów z form, czeka Pani aż te wszystkie elementy “zdębieją” i następnie zaczyna się faza klejenia?
Dokładnie. Wtedy odpalam Netflixa [śmiech].
Kiedy elementy są gotowe do klejenia zabieram się do pracy. Na przykładzie kubka, który wcześniej podałam, przyklejam uszka a następnie muszę te łączenia wyretuszować. Należy wygładzić miejsca łączeń – ja używam w tym celu gąbki, którą zacieram sobie wszystkie niedoskonałości. Po wyschnięciu można jeszcze raz wyretuszować, tak żeby pozbyć się już wszystkich niedoskonałości.
No i należy jeszcze zrobić dziurkę w takim uszku, bo w innym przypadku nie będzie odpowietrzenia i podczas wypału uszko może eksplodować.
PK: A czym skleja się te elementy?
Do łączenia wykorzystujemy tę samą masę, z której się odlewa. Ważne jest aby miała ona odpowiednią konsystencję, bo zbyt płynna będzie ściekać po elementach a zbyt twarda nie pozwoli na ich sklejenie. Po sklejeniu tych elementów
PK: Czy po sklejeniu produkt nareszcie ląduje w piecu?
Tak. To jest moment kiedy odbywa się pierwszy wypał, tzw. wypał na biskwit. Bardzo ważne jest, żeby przed włożeniem do pieca produkt był suchuteńki.
PK: Jaka jest temperatura wypału i jak długo trwa taki wypał?
To jest temperatura 900 stopni Celcjusza.
Jeśli chodzi o czas wypału to zależy w jakim piecu oraz jak bardzo jest zużyty. Jeśli piec jest stary trwa to dłużej niż w przypadku nowszego itd., ale zazwyczaj to jest około 10 godzin oraz kolejne 4 godziny kiedy piec stygnie.
PK: Załóżmy, ze temperatura jest odpowiednia i wyciągamy taki produkt z pieca. Jakie są kolejne kroki?
Potem wyciągnięciu produktu z pieca, retuszujemy go na sucho. Czyli papierem ściernym sobie wygładzamy całą ściankę produktu, w miejscach łączenia elementów lub tam gdzie istnieją inne niedoskonałości.
W przypadku moich produktów one są zazwyczaj matowe i nieoszkliwione, co wymaga, aby były bardzo dobrze wyretuszowane na sucho. Matowe produkty wymagają tego aby poświęcić im więcej czasu, ponieważ o wiele łatwiej można dostrzec ich ewentualne niedoskonałości.
Jeśli projekt ma być szkliwiony to robi się to na tym etapie. Istnieją różne techniki szkliwienia – ja stosuję technikę zanurzenia. To jest technika, która pozwala w szybki sposób równomiernie rozprowadzić szkliwo na całej powierzchni produktu.

Żeby było ciekawie, po szkliwieniu następnym krokiem jest odszkliwianie. Brzmi to nieco dziwnie, ale sęk w tym, że szkliwo nie może znajdować się na elementach, które będą stykały się w piecu z płytą piecową. Szkliwo które znajduje się na takich elementach, czyli na przykład na spodzie kubka, musi zostać usunięte.
PK: Dlaczego szkliwo musi być usunięte z tych elementów?
Szkliwo w zetknięciu z płytą piecową, może się po prostu do niej przykleić. Jeśli tak się wydarzy bardzo ciężko pozbyć się szkliwa z takiej płyty i czasami może to nawet oznaczać, że trzeba po prostu wymienić całą płytę. Te płyty są bardzo drogie, dlatego też pozbywamy się szkliwa aby ich nie uszkodzić.
Po usunięciu zbędnego szkliwa i odczekaniu do ponownego wyschnięcia produktów, możemy ponownie włożyć je do pieca.
PK: Jak długo musimy czekać tym razem zanim włożymy produkty do pieca?
Mniej więcej dobę. Także następnego dnia możemy już wkładać te produkty do pieca. Układanie produktów w piecu, również jest bardzo ważne. O ile przy wypale na biskwit możemy je układać jeden na drugim, o tyle przy wypale na ostro, czyli tym teraz, ze szkliwem produkty nie mogą się dotykać, więc mieści się ich w piecu znacznie mniej
PK: Ile trwa taki “wypał na ostro”?
Wypał na ostro to są minumum 24 godziny czekania.
No i to już jest w zasadzie koniec procesu – nasz produkt jest gotowy. Czasami wymaga jeszcze, jakichś minimalnych poprawek jak pozbycie się resztek substancji służącej do zabezpieczania płyty piecowej na której wypalamy produkt.
PK: Podsumowując, ile razy taki produkt ląduje w piecu i jak dużo czasu łącznie przeznacza się na jego wypał?
Produkt ląduje w piecu co najmniej dwa razy, natomiast w zależności od projektu i technik jego zdobienia to może być nawet do czterech razy. Większość, myślę, że ok. 70% z tych produktów które wytwarzam wypala się tylko dwa razy.

PK: Rzeczywiście jest to w takim razie bardzo długi proces – nic dziwnego, że nie podejmuje się Pani pochopnie zleceń indywidualnych.
Tak, szczególnie, że proces może być też bardziej skomplikowany, na przykład kiedy chcemy wypuścić na rynek produkt, który jest ma być wykorzystywany w kontakcie z żywnością.
Prawda jest taka, że żeby zrobić taki produkt, który nadaje się do wypuszczenia go na rynek należy bardzo dużo testować, sprawdzać i wszystko dopracowywać. To jest też czas kiedy testuję jak finalny produkt ma wyglądać wizualnie – dobieram kolor gliny, szkliwa, testuję fakturę itd.
Kiedy wprowadzam nowy projekt to jest to zazwyczaj około pół roku od kiedy taki pomysł pojawia się w mojej głowie do momentu gdzie mam już gotową formę i mogę taki produkt zacząć wytwarzać.
PK: Ile w takim razie zajmuje Pani zaprojektowanie nowego produktu?
Przy produktach z porcelany nie jest możliwe, aby w łatwy i szybki sposób wykonać choćby prototyp projektu, który klient mógłby zobaczyć. Długość i skomplikowanie tego procesu oraz fakt, że przy każdym nowym produkcie musimy sporo rzeczy testować sprawia, że takie zlecenia są też bardzo kosztowne.
PK: Prowadzi Pani pracownie już od 10 lat, czy zauważyła Pani jakieś zmiany na przestrzeni tych lat?
Największą zmianą na przestrzeni tych lat, jest to, że trzy, może cztery lata temu ceramika stała się niesamowicie popularna, co zdecydowanie działa na korzyść dla mojej pracowni. Jest bardzo dużo osób zainteresowanych takimi działaniami w zakresie ceramiki. Ludzie chcą brać udział w warsztatach, chcą próbować zrobić coś sami i przy okazji miło spędzić czas. Przychodzi do mnie też sporo par, które wolą spędzić wspólny czas tutaj, niż choćby oglądając telewizję. Wszyscy są zawsze bardzo zadowoleni, zarówno ze spędzonego w taki sposób czasu jak i pamiątki w postaci przedmiotów, które stworzyli.
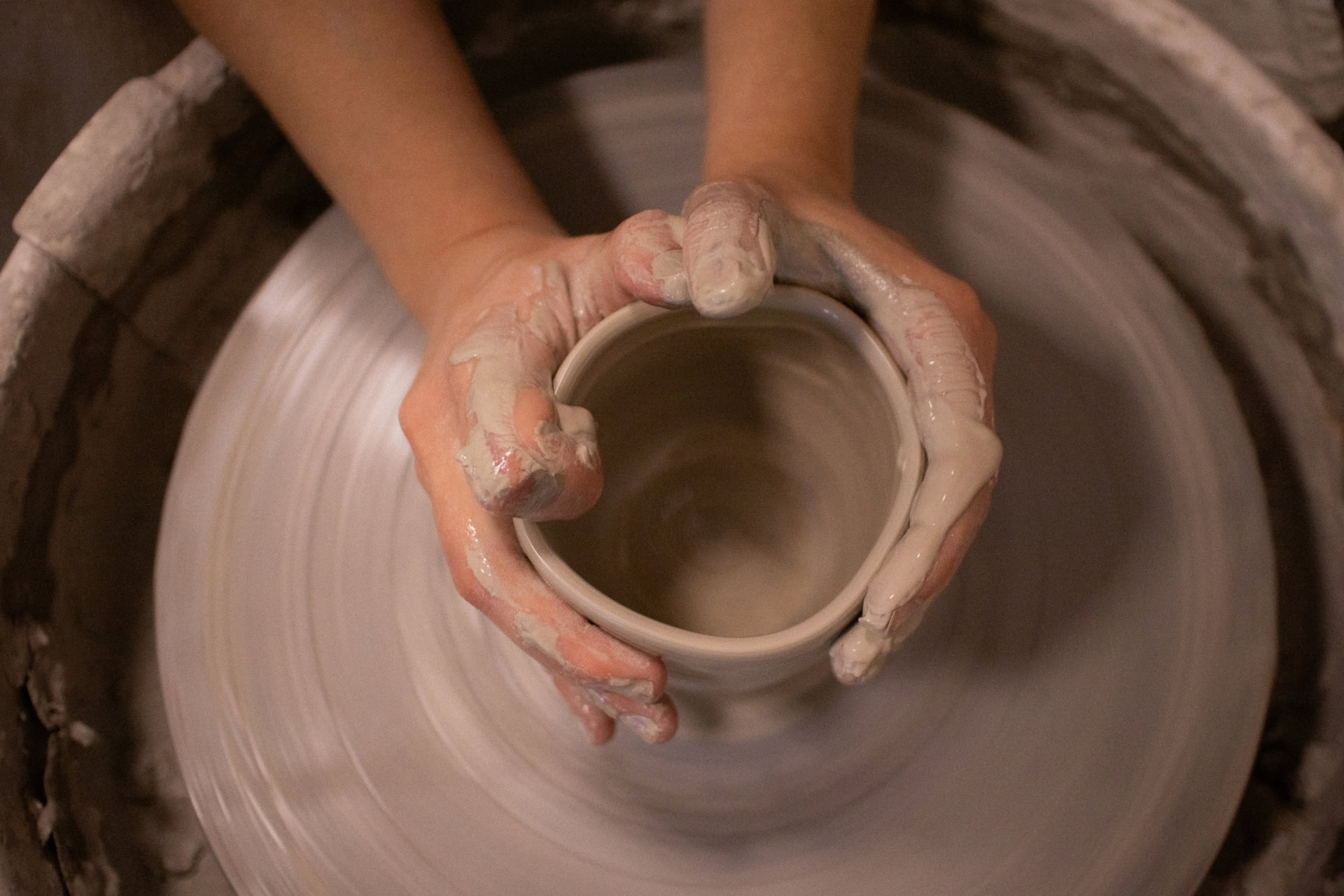
PK: Tacy ludzie wcześniej się nie pojawiali?
Wcześniej większość osób, która odwiedzała pracownie nie miała nic wspólnego z ceramiką, nie do końca wiedzieli w jaki sposób takie produkty powstają itd. Teraz klienci są bardziej świadomi – większość widziała gdzieś w mediach społecznościowych czy ogólnie internecie kogoś kto wytwarza produkty z ceramiki, często wiedzą, że są różne metody pracy z tym materiałem – to jest bardzo fajne.
PK: Czyli zmieniła się przede wszystkim świadomość klienta?
Tak, klienci są bardziej świadomi. To też wpływa na to, że już tak nie dziwi ich cena tych produktów, bo coraz częściej zdają sobie, przynajmniej w jakimś stopniu, sprawę jak powstaje taki produkt i ile jest to pracy. Wciąż jest jednak wiele osób, którym nadal wydaje się, że to jest bardzo proste.

PK: To pewnie wyzwanie z którym mierzy się wielu rzemieślników. Czy ma Pani jakieś rady dla młodych twórców, którzy chcą swoją pasję przemienić w zawód?
Trzeba być cierpliwym, wytrwałym i podążać za własnymi marzeniami.
PK: Czy ma Pani jakieś motto lub myśl, która Panią napędza?
Napędza mnie dobra zabawa. Robię to co robię, bo kocham to robić.