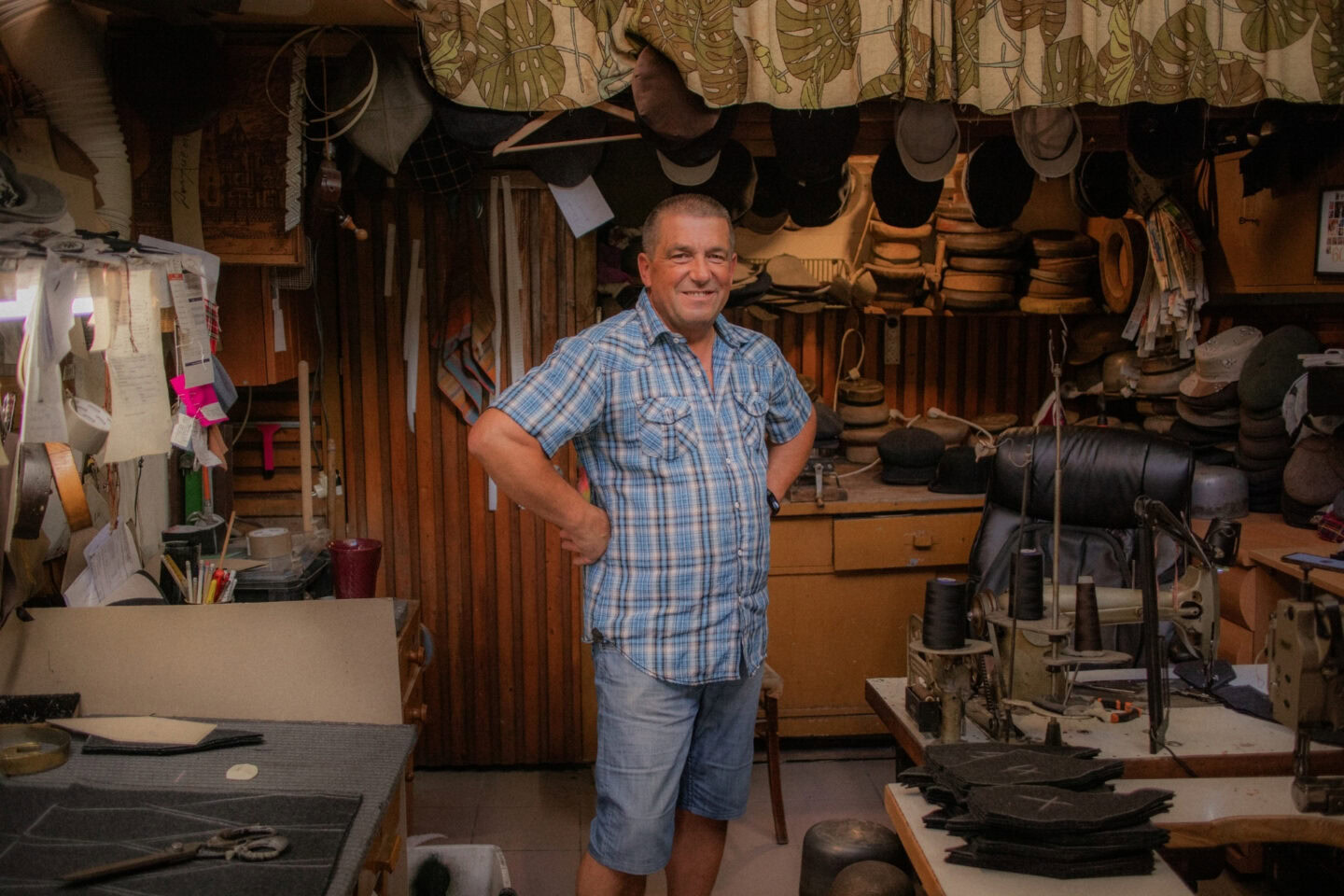
PK: Czy kiedy Pan zaczynał, spodziewał się Pan, że to stanie się Pana zawodem na całe życie?
Nie, zupełnie tak o tym nie myślałem. To miało być coś czym zajmuję się na chwilę jedynie po to aby pomóc rodzinie. Jednak bardzo to polubiłem i chciałem kontynuować. Uczyłem się więc tego zawodu, zdałem egzamin czeladniczy, a następnie egzamin mistrzowski. No i tak to zleciało. Szkoliłem się w tym zawodzie przez 4 lata. W tym roku minęły 24 lata mojej działalności. Niedługo będzie już fajny okrągły jubileusz, ale niestety nikt nie da mi premii. To zdecydowanie minus pracy na własny rachunek. [śmiech] Plus jest taki, że sam sobie jestem szefem, sprzątaczem i tak dalej.
PK: Czy może nam Pan powiedzieć kim są Pana typowi klienci?
Klienci są różni, tu nie ma reguły. Bardzo zależy to od danego sezonu. W tamtym roku, trafiło do mnie sporo młodych ludzi. Niektórzy przychodzą kupić coś konkretnego, inni odwiedzają mnie z ciekawości. Sporo młodych osób przychodzi z ciekawości a wychodzi z czapką lub kapeluszem.
Czapki są obecnie mniej popularne niż kiedyś. Myślę, że to w dużej mierze dlatego, że ciężko znaleźć takie, które są zrobione porządnie. Wielu ludziom podobają się czapki i kapelusze, ale kiedy nie znajdują takiej, która wygląda dobrze, często się poddają. Wielu klientów, kiedy dowiaduje się, że takie miejsce jak moja pracownia istnieje, chętnie przychodzą – chcą zobaczyć, sprawdzić i kupić coś w czym będą wyglądać dobrze.
PK: Czy są jakieś zasady dotyczące nakryć głowy?
Każde nakrycie głowy powinno być odpowiednio dobrane do twarzy. Nie wszyscy będą wyglądać dobrze w tym samym. Jeśli chodzi o odpowiednie dopasowanie czapki czy kapelusza, to jest to w dużej mierze praktyka. Bardzo ważne są tu proporcje. Źle dobrane nakrycie głowy może wpływać na to jak wygląda nasza sylwetka.
Kilka lat temu bardzo popularne były męskie kapelusze z dużym rondem. Miałem wtedy klienta, który był dość niski i planował zakup takiego właśnie kapelusza. Nie wyglądał w nim dobrze. Rondo kapelusza potrafi być dość przytłaczające i sprawia, że wyglądamy na niższych niż w rzeczywistości. Jeśli ktoś jest niski, to lepiej sprawdzi się mniejsze, podwinięte rondo.
PK: Doradza Pan swoim klientom?
Tak, zawsze sugeruję co może się sprawdzić a co niekoniecznie jest najlepszym wyborem. Jeśli klient potrzebuje rady to doradzam, natomiast oczywiście wybór należy zawsze do klienta.
Staram się, żeby klienci byli zadowoleni. W moim zawodzie bardzo ważna jest “poczta pantoflowa”. Choć w ostatnich latach, tę rolę po części przejmują media społecznościowe – szczególnie kiedy mówimy o młodszych odbiorcach.
PK: Czy klienci zawsze ufają pana radom?
Zazwyczaj tak. Ale czasem zdarza się, że w kwestiach takich jak dobór rozmiaru klient uważa, że wie lepiej. Wielu z nich później wraca i przyznaje mi racje.
Miałem takich klientów, którzy kupując lniane czapki, nie wierzyli mi, że taka czapka delikatnie się skurczy. Zakładali, że kiedy zaczną ją nosić to, wręcz przeciwnie, czapka się rozciągnie, więc wybierali mniejsze rozmiary. Len natomiast kurczy się od wilgoci. Kilka dni po zakupie wracali więc, prosząc o to, czy mogę im tę czapkę nieco rozciągnąć. [śmiech]
PK: Co najbardziej zaskakuje Pana klientów?
Klienci, którzy mnie odwiedzają, zazwyczaj są zaskoczeni kiedy dowiadują się, że to wszystko powstaje tutaj, na miejscu. Część z nich początkowo myśli, że ja jedynie sprzedaje nakrycia głowy. Nie wiedzą, że ja to wszystko robię sam.
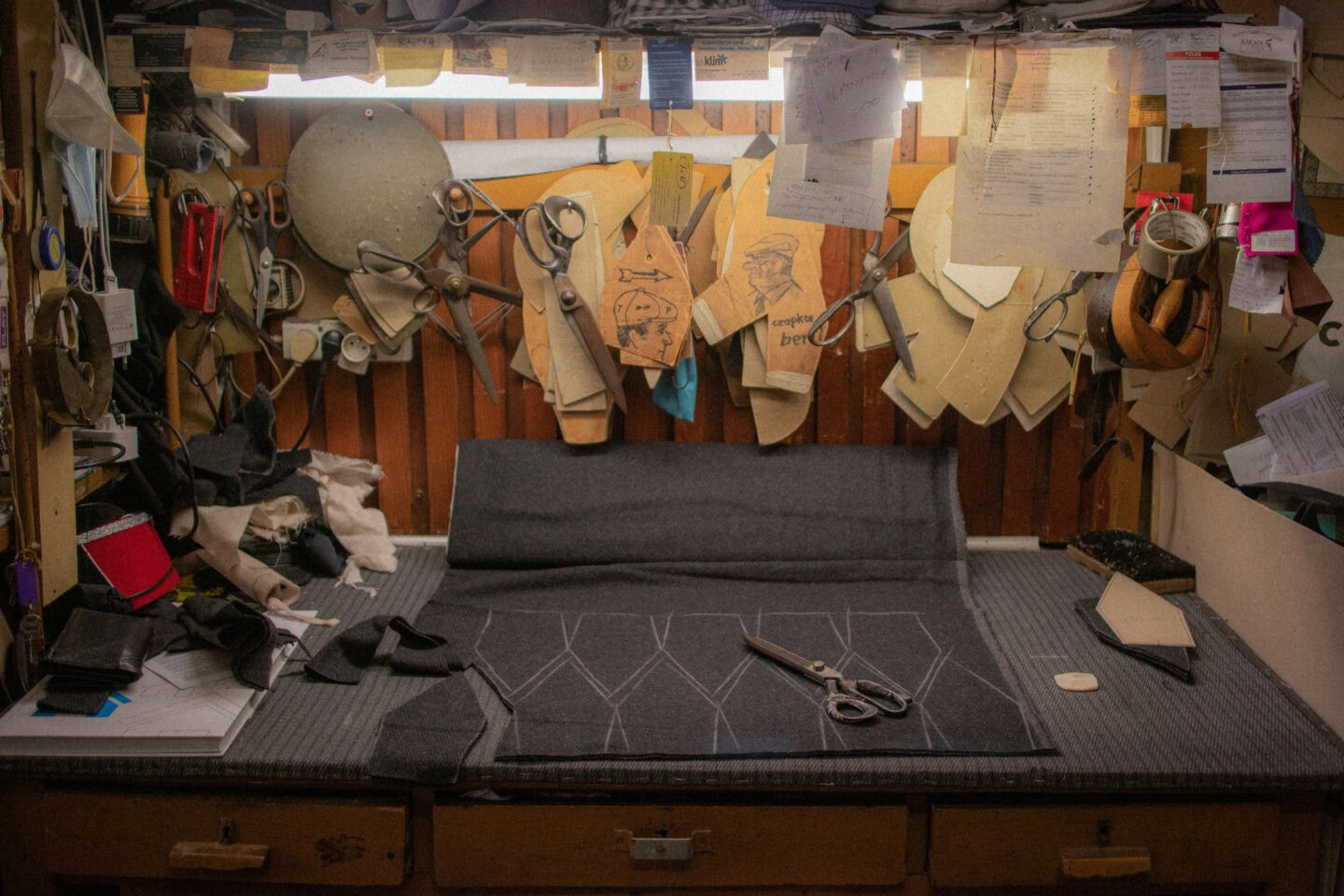
PK: Czy kiedy Pan zaczynał, spodziewał się Pan, że to stanie się Pana zawodem na całe życie?
Nie, zupełnie tak o tym nie myślałem. To miało być coś czym zajmuję się na chwilę jedynie po to aby pomóc rodzinie. Jednak bardzo to polubiłem i chciałem kontynuować. Uczyłem się więc tego zawodu, zdałem egzamin czeladniczy, a następnie egzamin mistrzowski.
No i tak to zleciało. Szkoliłem się w tym zawodzie przez 4 lata. W tym roku minęły 24 lata mojej działalności. Niedługo będzie już fajny okrągły jubileusz, ale niestety nikt nie da mi premii. To zdecydowanie minus pracy na własny rachunek. [śmiech] Plus jest taki, że sam sobie jestem szefem, sprzątaczem i tak dalej.
PK: Czy może nam Pan powiedzieć kim są Pana typowi klienci?
Klienci są różni, tu nie ma reguły. Bardzo zależy to od danego sezonu. W tamtym roku, trafiło do mnie sporo młodych ludzi. Niektórzy przychodzą kupić coś konkretnego, inni odwiedzają mnie z ciekawości. Sporo młodych osób przychodzi z ciekawości a wychodzi z czapką lub kapeluszem.
Czapki są obecnie mniej popularne niż kiedyś. Myślę, że to w dużej mierze dlatego, że ciężko znaleźć takie, które są zrobione porządnie. Wielu ludziom podobają się czapki i kapelusze, ale kiedy nie znajdują takiej, która wygląda dobrze, często się poddają. Wielu klientów, kiedy dowiaduje się, że takie miejsce jak moja pracownia istnieje, chętnie przychodzą – chcą zobaczyć, sprawdzić i kupić coś w czym będą wyglądać dobrze.
PK: Czy są jakieś zasady dotyczące nakryć głowy?
Każde nakrycie głowy powinno być odpowiednio dobrane do twarzy. Nie wszyscy będą wyglądać dobrze w tym samym. Jeśli chodzi o odpowiednie dopasowanie czapki czy kapelusza, to jest to w dużej mierze praktyka. Bardzo ważne są tu proporcje. Źle dobrane nakrycie głowy może wpływać na to jak wygląda nasza sylwetka.
Kilka lat temu bardzo popularne były męskie kapelusze z dużym rondem. Miałem wtedy klienta, który był dość niski i planował zakup takiego właśnie kapelusza. Nie wyglądał w nim dobrze. Rondo kapelusza potrafi być dość przytłaczające i sprawia, że wyglądamy na niższych niż w rzeczywistości. Jeśli ktoś jest niski, to lepiej sprawdzi się mniejsze, podwinięte rondo.
PK: Doradza Pan swoim klientom?
Tak, zawsze sugeruję co może się sprawdzić a co niekoniecznie jest najlepszym wyborem. Jeśli klient potrzebuje rady to doradzam, natomiast oczywiście wybór należy zawsze do klienta.
Staram się, żeby klienci byli zadowoleni. W moim zawodzie bardzo ważna jest “poczta pantoflowa”. Choć w ostatnich latach, tę rolę po części przejmują media społecznościowe – szczególnie kiedy mówimy o młodszych odbiorcach.
PK: Czy klienci zawsze ufają pana radom?
Zazwyczaj tak. Ale czasem zdarza się, że w kwestiach takich jak dobór rozmiaru klient uważa, że wie lepiej. Wielu z nich później wraca i przyznaje mi racje.
Miałem takich klientów, którzy kupując lniane czapki, nie wierzyli mi, że taka czapka delikatnie się skurczy. Zakładali, że kiedy zaczną ją nosić to, wręcz przeciwnie, czapka się rozciągnie, więc wybierali mniejsze rozmiary. Len natomiast kurczy się od wilgoci. Kilka dni po zakupie wracali więc, prosząc o to, czy mogę im tę czapkę nieco rozciągnąć. [śmiech]
PK: Co najbardziej zaskakuje Pana klientów?
Klienci, którzy mnie odwiedzają, zazwyczaj są zaskoczeni kiedy dowiadują się, że to wszystko powstaje tutaj, na miejscu. Część z nich początkowo myśli, że ja jedynie sprzedaje nakrycia głowy. Nie wiedzą, że ja to wszystko robię sam.

PK: To dla nich na pewno miłe zaskoczenie. Może nam Pan opowiedzieć jak wygląda ten proces?
Produkcja nakryć głowy zaczyna się od wyboru odpowiedniej tkaniny. Rodzaj materiału, którego użyjemy, jest w pewnym stopniu zależny od rodzaju czapki. Jest to ważne dlatego, że nie wszystkie materiały będą układać się w odpowiedni sposób.
Kiedy znajdziemy już tkaninę, należy za pomocą odpowiedniej formy wyrysować i wyciąć z niej elementy, które stworzą czapkę. Mam różne formy dla danych wzorów i rozmiarów. Te których używam, odziedziczyłem po moim wujku, który na każdej z nich rysował ludzi w nakryciach głowy.
Po wycięciu elementów z tkaniny, zszywam je na maszynie do szycia. Mam też inną maszynę, która służy tylko i wyłącznie do przyszywania daszków do czapek mundurowych. Trzeba też sprawdzić, czy po zszyciu czapka ma taki rozmiar jak powinna. Czasem minimalne przesunięcie przy zszywaniu elementów skutkuje tym, że czapka jest za mała lub za duża. Po zszyciu, wszywamy podszewki i inne elementy występujące w danym modelu.
Kiedy już wszystko jest na miejscu, to nabijamy taką uszytą czapkę na specjalny klocek. Klocki mają różne rozmiary, więc dobieramy odpowiedni do rozmiaru czapki. Te klocki składają się z kilku części, więc po wybraniu odpowiedniego rozmiaru, łączymy wszystkie jego elementy – tak jakby to były puzle. Potem nakładamy czapkę na klocek i zabieramy się za prasowanie.
Najpierw prasujemy zewnętrzną część czapki za pomocą żelazka. Do wyprasowania środka, potrzebna jest nam już specjalna maszyna. Dzięki prasowaniu wnętrza, wiemy, że wszystkie elementy wewnątrz są ułożone prawidłowo i nic później klienta nie będzie gniotło.
Jeśli czapka ma jakieś daszki i tak dalej, to oczywiście też trzeba to wszystko porządnie przyszyć. Ale to cała filozofia. Później, zostaje już tylko czekać na klienta, który tę czapkę kupi.
PK: Czy w przypadku kapeluszy ten proces bardzo się różni?
Tak, ten proces wygląda inaczej. W przypadku kapeluszy, proces polega przede wszystkim na modelowaniu materiału w taki sposób, aby osiągnąć kształt odpowiedni dla danego modelu. Modelowanie takiego materiału, zaczyna się od naciągnięcia go na specjalny stożek. Uzyskanie właściwego kształtu wymaga sporo wprawy i doświadczenia, trudno to tak po prostu opisać.
Kiedy uzyskamy już odpowiedni kształt, należy odczekać, aż kapelusz wyschnie. Jeśli jakiś fragment zostanie mokry, to później będzie się on odkształcać. Takie schnięcie zazwyczaj trwa około doby. Później obcina się rondo, wykańcza podszewki i dodaje wstążki czy inne dekoracje.
PK: A co sprawia, że taki kapelusz zachowuje swój kształt?
To tajemnica! [śmiech]
Na pewno nie lakier do włosów. Jakiś czas temu przyszła do mnie Pani, która chciała żebym odparował jej kapelusz. Kiedy tylko puściłem parę, kapelusz zrobił się cały biały. Okazało się, że Pani wyczytała w internecie, że lakierem do włosów można właśnie usztywnić kapelusz, więc przed przyjściem do mnie, spryskała go takim lakierem.
Niestety, internet nie zawsze pomaga.

PK: Mówił Pan o odpowiednim doborze materiałów. Z jakich materiałów korzysta Pan tworząc swoje produkty?
Są to przede wszystkim naturalne tkaniny. Do letnich nakryć głowy wykorzystuję przede wszystkim bawełnę i len. Przy zimowych, korzystam z wełny. Przy niektórych specjalnych czapkach, jak te studenckie, wykorzystuje się aksamit. W tym przypadku korzystam z polskiego aksamitu, który jest wykonany z bawełny. Mam już wiele sprawdzonych materiałów.
PK: Niektóre czapki mają też inne elementy, na przykład metalowe. Skąd bierze Pan te elementy?
Jeśli chodzi o elementy skórzane, różne sznurki i tak dalej to nie ma problemu z zamówieniem takich elementów. Część z nich kupuję po prostu w różnych pasmanteriach. Największym wyzwaniem jest pozyskanie elementów metalowych – często potrzebuję konkretnych wzorów, które trzeba robić na zamówienie. Na szczęście udało mi się znaleźć takiego gościa – rzemieślnika, który zajmuje się wytwarzaniem rzeczy z metalu. Obecnie to on robi mi te elementy na zamówienie. Współpracuję też z innymi rzemieślnikami.
PK: Działa Pan już od wielu lat. Czy materiały i typy nakryć głowy bardzo się w tym czasie zmieniały?
Moda zawsze się troszkę zmienia, ale generalnie wszystko kręci się w kółko. Kształty też ulegają zmianie. Raz modne są szersze, raz węższe, czasem jeden kolor a czasem inny i tak dalej. Ale to nie są duże zmiany, bo kaszkiet to jest kaszkiet, nie ma co tu za bardzo zmienić. Zresztą moda na to, co nosiło się kiedyś, prędzej czy później też powraca.
Nie wiem co będzie modne w następnym sezonie. W tamtym sezonie na topie były kaszkiety
PK: Skąd nagła popularność kaszkietów?
Ten fason czapek na nowo wypromował popularny serial Peaky Blinders. Do tego stopnia, że miałem paru klientów, którzy prosili mnie o wszycie do takiego kaszkietu żyletki – tak aby naśladować to co robili bohaterowie serialu. Oczywiście to nie była prawdziwa żyletka. To był taki grubszy metalowy odlew, który nie był ostry i jedynie odwzorowywał kształt żyletki.
PK: Czy pop kultura często wpływa na to jakich nakryć głowy szukają Pana klienci?
Tak, zdecydowanie.
Często trafiają do mnie ludzie, którzy zobaczyli jakiegoś artystę czy muzyka w danej czapce i szukają czegoś podobnego. Jeśli nie mam czegoś takiego w ofercie to czasem pytają czy podejmę się zrobienia takiej czapki.


Podejmuje się Pan takich zleceń indywidualnych?
Jeśli jestem w stanie, to zrobię, jeżeli nie jestem w stanie, no to nie zrobię. Zawsze przy takich zleceniach informuję klienta, że jest ryzyko, że finalny produkt nie będzie wyglądać i układać się dokładnie tak jak referencja, którą mi pokazuje. Klienci czasem nie zdają sobie sprawy, że zależnie od wykorzystanej tkaniny, taka czapka będzie się różnie układać. Dlatego ciężko jest zrobić coś na przykład na podstawie zdjęcia.
Robię też czapki dla teatrów, na rekonstrukcje i dla uniwersytetów. W tych przypadkach często wzoruję się na zdjęciach. Jeśli to tylko możliwe staram się obejrzeć podobne egzemplarze na żywo. Czasem kiedy odtwarzam historyczne nakrycia głowy, odwiedzam muzea, żeby lepiej przyjrzeć się modelom z danego okresu. Wtedy staram się patrząc na takie czapki czy kapelusze, “złapać” ich wymiary oraz proporcje. Czasem nawet coś sobie wstępnie na ich podstawie szkicuję. Teoretycznie można napisać pismo do kustosza, z prośbą o wyciągnięcie takiego eksponatu z gabloty, ale czas oczekiwania jest długi i nie mam gwarancji, że taką zgodę dostanę.
PK: Wspomniał Pan czapkach dla uniwersytetów. Czy może Pan opowiedzieć coś więcej na ten temat?
Dawniej była taka tradycja, że każda uczelnia miała swoje czapki studenckie. Trochę o tym zapomniano i wiele uczelni przez lata z nich nie korzystało. W ostatnim czasie polskie uczelnie zaczynają wracać do tej tradycji. Szukają w archiwach wzorów i kolorów czapek, które nosili studenci.
Na Uniwersytecie Jagiellońskim jest aż 18 kolorów takich czapek. Inny kolor dla każdego wydziału. Każdy odpowiadający todze danego dziekana. Działa tam nawet tak zwane Bractwo Czapki Studenckiej, z którym współpracuję.
Obecnie tworzę takie czapki dla kilku uniwersytetów w Polsce. Współpracuję min. ze wspomnianym już Uniwersytetem Jagiellońskim, Uniwersytetem Śląskim oraz Politechniką Krakowską.
PK: Czy Pana praca i proces tworzenia czapek i kapeluszy zmieniły się przez te 24 lata kiedy prowadzi pan działalność?
Rozpocząłem działalność 1990 roku.
Ten proces, wygląda tak naprawdę tak samo jak wiele lat temu. Robię czapki i kapelusze w taki sam sposób jak przodkowie. Oczywiście, maszyna do szycia nie jest już na pedały, tylko jest elektryczna, tak jak i żelazko, które dawniej było na duszę. Poza tym nic się nie zmieniło. Nic więcej tu nie wykombinujemy, bo to praca naszych rąk i trochę inwencji. To co się zmienia to popularność tego zawodu. Kiedy zaczynałem się go uczyć, w Krakowie było ponad 10 czapników. W tej chwili zostałem sam.
Zauważam natomiast, że ludzie już nieco przejedli się chińszczyzną i “sieciówkami”. Widocznym trendem jest to, że klienci wracają do zakupów w mniejszych, lokalnych pracowniach. Coraz więcej jest osób, które są w stanie zapłacić więcej, żeby mieć coś, co jest zrobione indywidualnie dla nich. Zobaczymy czy ta tendencja się utrzyma – czas pokaże.
PK: Opowiedział nam Pan sporo o różnych nakryciach głowy, które pan wytwarza. Czy są takie, które szczególnie lubi Pan tworzyć?
Lubię swoją pracę, więc praca nad wszystkimi czapkami i kapeluszami sprawia mi przyjemność.

PK: Czy niektóre są trudniejsze w wykonaniu niż inne?
Każda jest prosta do zrobienia, jeśli wie się jak to zrobić. Tak samo każda jest trudna, kiedy robi się ją po raz pierwszy. Kiedy nie ma się żadnej formy, trzeba kombinować i testować różne rozwiązania.
PK: A czy pan również nosi nakrycia głowy na codzień?
O tak! Jak zawsze jestem pierwszą osobą, która zakłada czapkę gdy zbliża się jesień i ostatnim kto ją zdejmuje gdy przychodzi wiosna.
PK: Czy chciałby Pan coś przekazać młodym twórcom, którzy chcą zajmować się taką kreatywną, rzemieślniczą pracą?
Cierpliwości. Dobry wynik przyjdzie z czasem. Nie da się wszystkiego zrobić od razu.